In the workplace today, many employees must complete EHS tasks such as daily forklift inspections, monitoring forms, looking up SDS sheets, and shipping and receiving using shared devices. Electronics are often considered “high touch” items and can be a significant source of exposure when shared amongst employees. Limiting risk can come in many forms.
The American Journal of Medicine reports that the cost of even a single worker testing positive for COVID-19 can have significant financial impacts for employers with conservative estimates showing the employer financial loss at $4,000 per worker for each worker who gets sick. With the added financial risk, workstream disruption, and impact on employee health and wellness, investing additional time and thought into how you reduce exposure for shared workstations is one small step that you can take to significantly reduce the risk of exposure and infection in your workplace.
Tip 1: Reduce the Need for Shared Devices by Extending Access to Personal Devices
One easy way to improve access to EHS information and limit the risk of exposure from shared workstations is to provide access to common EHS forms, data, and tasks on assigned or personal devices. One such way to do this is using EHS software that puts your EHS documentation and the ability to complete checklists, monitoring activities, and tasks at your employee’s fingertips.
Things to Consider:
- Permissions & Security
When considering this option, the first thing you should consider is how you will permission access to the application you will use. Selecting a system that allows for granular permissions allows you to control the level of access each employee has to your data and functionality within the application and ensures that you can extend access safely and securely. - Enablement
Next, you will want to consider how you will enable your workforce. Look for systems that offer on-demand access to help content and training resources for your team. In-app help is a great way to provide context to the person completing an EHS task on the screen where they are currently working. This ability sets some EHS applications apart from off-the-shelf solutions including commonly used file sharing or office applications. - Communication
In addition to enabling employees to complete tasks that may typically be done on a shared workstation or using printed forms, EHS applications can provide you with additional communication tools including proactive reminders for past-due tasks and the ability to send email and SMS text messages to your team. When evaluating EHS applications, it is prudent to look for the solution that enables you to communicate more effectively and efficiently. - Visibility
Finally, you should consider how you – the EHS Manager, will have access to see the status of tasks and actions taken in the application. How will you know that each employee is completing assigned tasks? How will you ensure that you are minimizing your audit risk by reviewing and approving completed activities? In selecting a system that meets your needs, you should look for an application that logs user actions (such as who created or modified a record) and allows you to view outstanding items so that you can follow up with employees who may need additional training or guidance on how to complete their tasks.
Tip 2: Update Sanitization Procedures for Shared Devices
In some environments, enabling users to use an assigned or personal device may not be feasible. When this is the case, you should consider the shared workstations that present a risk from being a “high touch” item and minimize the risk by implementing routine cleaning and disinfecting of electronic surfaces in common or shared areas.
Things to Consider:
- Procedure
In order to ensure that common workspaces are regularly sanitized, you will want to consider your current procedures to determine where you can update or add requirements and instructions for cleaning shared workspaces and electronics. Once such place may be in your Workplace Hygiene Policy. - Responsibility
Be sure to assign responsibility for cleaning shared workspaces. Ideally, to minimize the risk of exposure, each employee should be responsible for cleaning and sanitizing the workstation when they are done using the device. - Sanitization Process
Consider the steps that you would like employees to take to properly sanitize shared electronic devices. Be sure to select a cleaning product on the EPA List N that meets the manufacturer’s recommendations. We’ve included a sample procedure for cleaning electronics using Isopropyl Alcohol below to help you get started. - Materials
Finally, gather the materials that are needed to effectively clean and disinfect the shared workspace. You may want to consider putting a wipeable cover on electronics to make cleaning and disinfecting easier. You can also get USB caps or covers to limit the risk that moisture from cleaning enters the ports of the device.
Sample – Guidelines for Cleaning Shared Electronic Devices
- Power off the device (when possible) prior to cleaning.
- Take a clean microfiber cloth from the bin of cleaning cloths.
- Put on a new pair of disposable nitrile gloves.
- Moisten a microfiber cloth with a mixture of 70% isopropyl alcohol/30% water. Do not use paper towels or other fibrous materials.
- Carefully wipe the screen of the device with the moistened cloth in one direction moving from the top of the display to the bottom.
- Wipe the keyboard, inner housing, and outer housing of the device using the moistened cloth. Use care to avoid getting liquid into ports or openings on the device.
- Wipe the control panel of any printers at the workstation using the moistened cloth.
- Wipe the peripherals (external keyboard, mouse, headset, etc.) at the workstation using the moistened cloth.
- Wipe the desk and any other surfaces in the shared workstation using the moistened cloth.
- Put the moistened cloth in the bin of soiled cleaning cloths so that it can be laundered before future use.
- Put the used nitrile gloves in the trash.
- Ensure surfaces have completely air-dried, with no visible moisture, before turning the device on after cleaning. EPA testing indicates alcohol needs a 5-minute dry time to be effective.
Chemical Safety Information
Chemical | Potential Hazards | Controls |
Isopropyl Alcohol | · Highly flammable · Capable of forming explosive vapor/air mixtures · Alcohols may de-fat the skin and cause dermatitis · Inhalation of concentrated alcohol vapor may cause irritation of the respiratory tract and have effects on the central nervous system · May cause drowsiness or dizziness · Contact with eyes may cause serious eye damage/eye irritation | Disposable nitrile gloves Use in well-ventilated areas away from ignition sources |
Highlights from the CDC’s Guidance on Cleaning and Disinfecting Your Facility
The CDC released guidance, last updated in June 2021, on cleaning and disinfecting your facility to reduce the risk of infection from COVID-19.
First, consider when to clean and when to disinfect. For areas that are “low touch” cleaning may be sufficient. In areas that are “high touch” or areas where there is a high transmission rate of COVID, low vaccination rate, infrequent use of prevention measures, or where the space is used by people with increased risk for severe illness, disinfection (or sanitization) is recommended.
To get started with updating your cleaning/disinfecting plan throughout your facility, the CDC recommends the following steps developing a plan including determining what needs to be cleaned and the resources and equipment needed. Once you have a plan, you’re ready to implement – the CDC recommends cleaning “high touch” surfaces at least once a day and disinfecting when needed.
Alternative Disinfection Methods
There are several alternatives on the market that can be used to sanitize items. When considering alternative methods to cleaning and disinfecting, it is critical that you “do your homework” to ensure that the method you are considering is effective.
- Ultrasonic waves, high intensity UV radiation, and LED blue light has not been fully established against the virus that causes COVID-19.
- The CDC does not recommend the use of sanitizing tunnels and there is no evidence suggesting that they are effective in reducing the spread of COVID-19. The chemicals used in these tunnels could cause skin, eye, or respiratory irritation or injury.
- In most cases, fogging, fumigation, and wide-area electrostatic spraying are not recommended as primary methods of surface disinfection and come with several safety risks to consider.
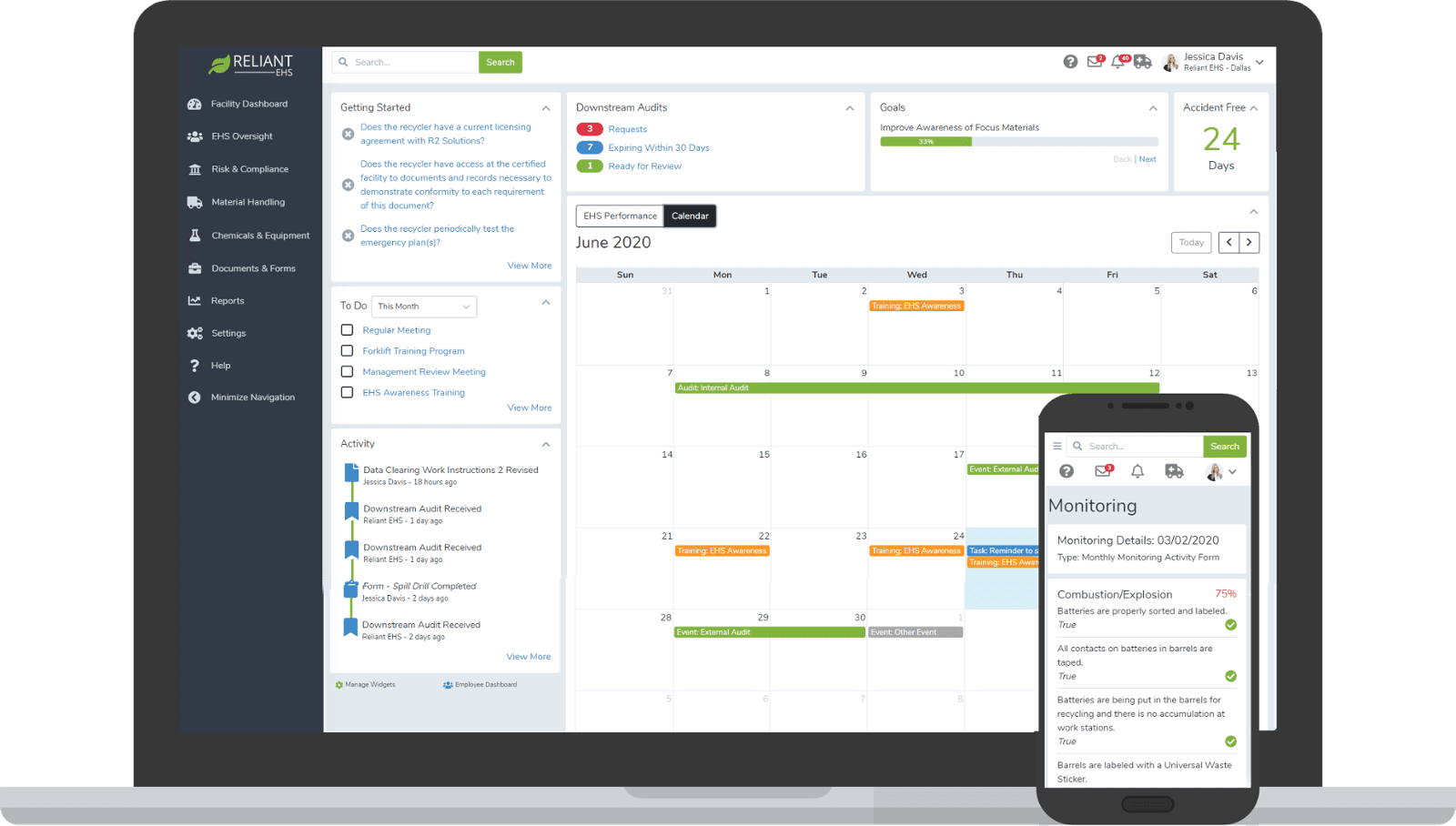
Let us show you why EHS managers choose Reliant EHS.