We often hear about EHS KPI’s, leading and lagging indicators, and other safety metrics but what do they mean for our businesses? How do we determine what is meaningful to track without adding additional administrative work for our EHS staff?
When we look at examples of EHS KPIs, they all seem to measure generic safety criteria or are slanted toward high risk industries, which typically do not fit most processors or recyclers in the e-waste industry.
This begs the question, what should we measure and how do we determine what is most important to us, our employees, our customers, and the overall success of our businesses?
What makes a winning KPI?
First, let’s explore the characteristics of a good KPI. KPI’s should be tailored towards your business and act as a point of reference to demonstrate to all stakeholders that your company is moving towards clearly defined and common goals. For a KPI to be effective in making your organization “SAFER”, it should have the following characteristics:
- Simple and important
- Aligned with your business
- Focused and high impact
- Exempt from financial metrics
- Regularly measured
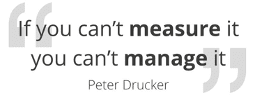
Let’s take a deeper dive into each of these characteristics and what they mean.
How do I know if my KPI "fits"?
A good set of KPI’s must be considered in the context of your business environment. Let’s take a quick look at some common trends in the e-waste industry.
Change is constant!
Whether the change results from high employee turnover, variations in skilled labor, changes in the regulatory landscape, shifting auditor expectations, client SLAs, or changes to devices we process, we know that change is the one thing we can count on. The expectation of constant change creates compliance and performance challenges for us to overcome.
Manual processes are prevalent...and they're costing you
What do we do in response to change? Unfortunately, when EHS staff must constantly respond and adapt to change rather than proactively anticipating and managing change manual processes become the go-to solution. Because manual processes for EHS are so common in our industry, audits and demands for high levels of data collection can slow the formation of business relationships resulting in longer sales cycles, stalled sales channels, and reduced ability to respond to changes with agility. These processes are not only inefficient for EHS teams, they have a ripple effect through the business and eventually end up hitting the bottom line.
EHS starts to be looked at as less of an operational center of excellence, and more of as a necessity to remain competitive and compliant. EHS staff are often forced to focus on essential compliance activities rather than focusing beyond compliance, into operational excellence and performance, placing both on an equal footing resulting in increased value delivery to their organizations.
So how do we fix it? The solution lies in sustainability
Right, this is an article about the e-waste industry…we all know about sustainability, but when it comes to using KPIs to create a sustainable program, the concept may seem a little foreign. The concept of sustainability we are referring to is program sustainability – an environment where the business views the EHS function as a key asset for building and maintaining profitable growth along with contributing net value to the environment, staff, customers, the community, and the world.
The idea of the “triple bottom line” indicates that there should not be tradeoff between doing good and doing well, and a commitment to wholistically serving the needs of our customers rather than just selling a product. This is exemplified in the e-waste industry in the commitment so many have made to integrating R2, RIOS, e-Stewards, and WEEE standards into the fabric of business operations.
To create a sustainable program that delivers on the “triple bottom line”, we must empower EHS managers by providing visibility to the positive impacts that the EHS program has created. Using KPIs creates a clear and tangible way to highlight EHS performance, create accountability, and engage your team in aligning personal and operational behaviors.
Defining KPIs for the e-waste industry
So now that you have a better understanding of what makes a winning KPI and how creating and celebrating KPI successes can impact your business, let’s look at a few KPIs that you can implement to measure your company’s EHS performance.
From written KPIs to action
Once you have defined a set of KPIs, keeping in mind you’re the qualities of a SAFER KPI and the right “fit” for your company, you need to translate your metrics into actions that drive EHS and operational performance and behaviors.
Ready, Set, Goal!
As you were defining your KPIs, it is only expected that you did so with goals in mind. Goals to have everyone respond correctly to your next fire drill or to have all your corrective actions resolved within 30 days. These goals or targets are a great starting point, however, to keep your team aligned and moving forward, it is important to focus on measurable and iterative improvements that, supported by your KPIs, help employees see meaningful change.
For each of your identified KPIs, you should think about who within your organization will be accountable for measuring the KPI each month and who can lead the charge on improving performance. These individuals are your KPI and goal owners.
This is a great opportunity to engage members of your staff in the EHS process that may not otherwise play a leading role. For example, consider partnering a senior staff member or executive sponsor as the KPI owner with a more junior team member as the goal owner. This results in improved engagement and creates a sense of ownership across organizational levels.
Defining Responsibilities
Your KPI owner and goal owner will work closely together to measure the KPI and determine how it can be improved through goals that individuals and departments within the company can work towards.
The KPI owner should:
- Define the criteria for measuring performance of the KPI
- Define the cadence for measuring performance of the KPI
- Create a defined and repeatable process for measuring and reporting performance
- Define actions (goals) the company can take to improve KPI performance
The Goal owner should:
- Promote the goal within the company
- Recruit other staff members to participate in reaching the goal
- Determine what actions the company can take to reach the goal and assign responsibility for those actions
- Track and measure progress towards the goal
- Report goal performance back to the KPI owner
Implementing KPIs without increasing administrative overhead
Does the thought of creating KPIs and goals that enable your company to continually improve sound great on one hand, but also like a lot of work? We talked about the drain that manual processes have on EHS programs and the last thing you want to is introduce KPIs that create even more manual tracking.
Reliant EHS is here to help with solutions designed to improve your program efficiency (and, you guessed it – tracking goals and KPIs is included). Contact us to talk more about how Reliant EHS can help you go beyond compliance.
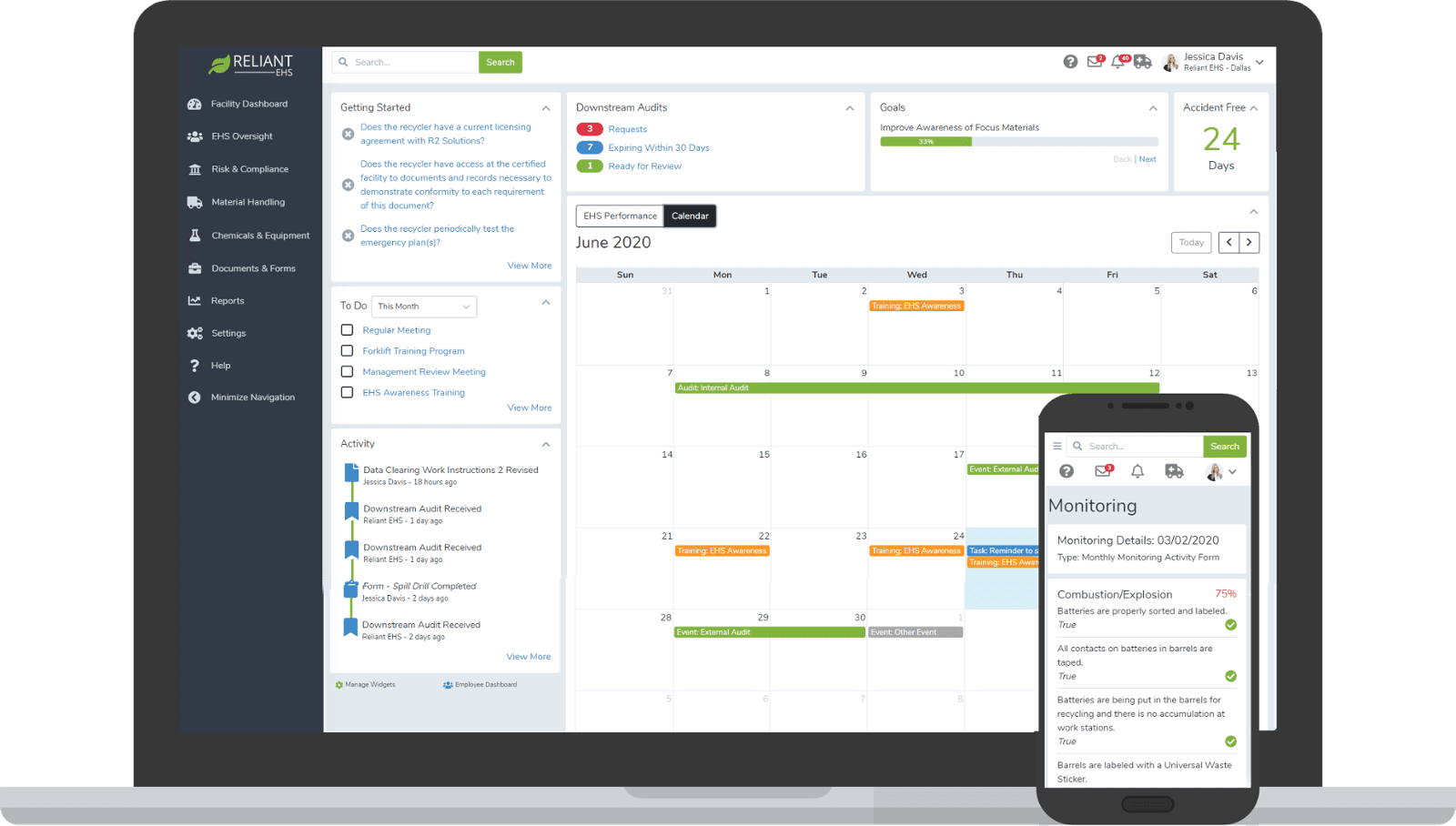
Let us show you why EHS managers choose Reliant EHS.